Textiles, Beauty Products, & Home Goods (The Century of Biology: Part II.VI)
A parallel evolution to that changing how the products listed above are made is happening with consumer products. These efforts are also being made to reduce emissions and transition away from oil- and animal-derived products. After all, our current faux leathers called “pleather” are made with plastics. Alongside these reasons, research into bio-based textiles is propelled by the possibility of inventing new materials with improved performance characteristics. Companies like Spiber are manufacturing spider silk at scale, a material with unique strength for its weight and that can’t be made like traditional silk because spiders will eat each other when in close contact. Finally, other companies like Gingko are looking to replace the sometimes shockingly inefficient production processes of dyes and fragrances. As an example, a red dye called carminic acid used in food products like Air Heads and Yoplait yogurt is made by smashing up 70,000 cochineal bugs to yield 3 oz of the dye. Scientists grew the dye directly by reserve engineering the bug’s enzymatic pathway and then mimicking it in engineered microbes.[1]
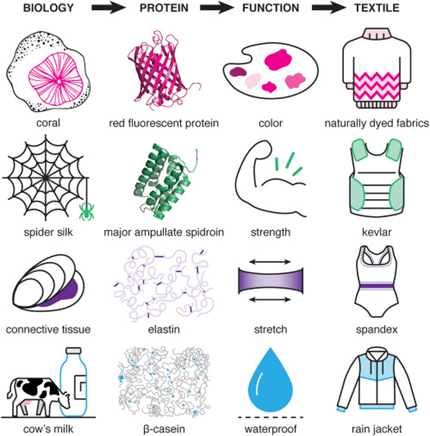
Spider Silk:
An excellent paper released in Cell in September made some great progress in the field. It unraveled the molecular chemistry explaining the tradeoff between (hint: it has to do with hydrogen and non-covalent bonds) and used that to explain why spider silk is both stronger than Kevlar and has greater tensile strength than nylon. It then introduced the latest model of the silk’s minimal structural unit. As its finale, it used CRISPR-Cas9 to create the first genetically modified silkworm capable of spinning the whole spider silk. The resultant silk fibers exhibit remarkable characteristics, including high tensile strength (1,299 MPa) and ultra-high toughness (319 MJ/m3). Here’s some more detail on spider silk:
The mechanical properties of both silk and spider silk are determined by their protein quaternary structures, which are influenced by both primary protein structure and spinning processes. However, due to an incomplete understanding of the spinning mechanisms and the intrinsic nature of silk fiber toughness and strength yet to be unraveled, even the most advanced microfluidic spinning techniques fail to replicate the physicochemical environment required for natural silkworm silk and spider silk spinning. Consequently, most synthetic spider silk fibers currently available exhibit inferior mechanical properties in one or more aspects compared with their natural counterparts. Moreover, due to the inherent challenge of replicating the protective “cuticle layer” found in natural silk and spider silk, the maintenance duration of the mechanical properties in artificial spider silk and regenerated silk fibers is significantly shorter compared with their natural counterparts. In fact, in our laboratory, wet-spun spider silk experiences a significant decline in mechanical properties within a few weeks.
The silk glands of domestic silkworms and spider silk glands exhibit remarkably similar physicochemical environments. Therefore, by leveraging the high-density cultivation of domestic silkworms for spider silk production, we can overcome the scientific challenges associated with the yet-to-be-fully-deciphered spinning mechanism of spider silk and the technical hurdles in developing spinning processes. This approach also enables us to address the engineering obstacles involved in achieving low-cost, large-scale production of spider silk.
Here are two of the main companies in the space:
[2]Most people wouldn’t pay $230 for a T-shirt or $1,375 for a parka. But when the North Face Japan put a limited number of these items on the market in 2019, they quickly sold out. The reason: they were made with fiber supplied by Spiber.
Founded in 2007, Spiber produces its novel material in very small quantities at a plant in Japan, which explains why the North Face products were so expensive. Spiber wants to change that using the more than $640 million it has raised from investors. It just opened a plant in Thailand that will use sugarcane to produce several hundred metric tons of Brewed Protein a year and plans ten times the size in Iowa. The company claims these plants will allow it to reach $100 per kg and then approach that of wool and silk.
The Noth Face Moon Parka was delayed several years because of problems when the material got wet. solved the problem by studying nature, Sekiyama says. Spiber researchers took a closer look at the protein in spider silk and identified the amino acids that are responsible for the supercontraction. They then changed the amino acid sequence to create a new gene that, when inserted in bacteria, generated a material that doesn’t shrink when wet.
They have also developed concepts for fiber-reinforced materials with Toyota group companies for use in car doors instead of steel that are lighter and better shock absorbing. In that same project, they also developed polyurethane composite foam for car seats with Bridgestone, the tire maker.
“Our technology allows us to simulate, in parallel, changes and evolution in the natural world within a laboratory,” Sekiyama says. “We make a tremendously large number of candidate molecules, pick out apparently suitable ones, find out the most promising DNA sequences among them, and push ahead with new generations of the relevant excellent DNA.” Only Spiber has the ability to do that with structured protein at ultrahigh speed, he claims.
The new material, Brewed Protein, is quite different from, and more versatile than, synthetic spider silk, Sekiyama says. Consumers perceive fiber made from Spiber’s material as high end not only because of its performance and biodegradability but also because of its feel.
In blind tests conducted by third parties in Japan and the US, “a majority of the participants said that Brewed Protein felt and looked better than cashmere wool.”
[3]Founded in 2008, AMSilk’s beachhead market was as high value, low volume gels for cosmetics products. By 2017, their gel was already in 20 specialty cosmetics products. Early on, they also developed Medtech applications including a coating for breast implants, tested in vivo in preclinical trials, where the spider silk gel’s biocompatibility lowered inflammation and other post-procedure problems. Their fiber can be used for biosensors and even in 3D printable structures. By focusing on non-fiber applications, they avoided the challenges of material fabrication we spoke about earlier.
In 2015, AMSilk made their first fiber, branded as Biosteel. In the past few years, they’ve started partnering with several large companies and have multiple products in the market. Airbus is researching how to replace carbon fiber with AMSilk's fiber in composite parts on their airplanes. This would allow for planes to better withstand impacts. Airbus's Innovation Manager said this about spider silk:
We haven’t even begun to scratch the surface here. Ultimately, this material could enable us to approach design and construction in an entirely new fashion.
It bends without losing strength. So, it could be integrated on parts away from the fuselage that are prone to debris impact or bird strikes. It could help protect space equipment in a similar manner or be applied to defence products.
Omega launched a commercial watch strap line using AMSilk's Biosteel that is 30% lighter and hypoallergenic. Adidas has been developing a shoe upper with them and Mercedes is exploring using Biosteel in interior parts. To focus on these and other products in their pipeline, in 2019 AMSilk sold their cosmetics business to Givaudan, the world's largest flavor and fragrance company.
AMSilk is scaling capacity from 1 ton last year to 6 tons this year and are aiming for several thousand tons of capacity by expanding their CMO network beyond Europe.
Mycelium Leather:
- Mycelium, the “root structures” of certain species of mushrooms and other fungi, is another biomaterial scaling up fast. In particular, the startup Ecovative produced 45 tons per year in 2021 for a growing range of uses and can double capacity.
Modern Meadow, a producer of ‘biologically advanced materials’ has developed sustainable biofabricated materials inspired by leather. They partner with Evonik, the major company of speciality chemicals, to bring its production to commercial scale. The leather’s main component is microbially fermented collagen, the main structural component in cow hides.
Two other biomaterials examples:
- Humble Bee Bio is working on performance biopolymers inspired by the solitary Australian masked bee. The bee produces a polymer that is resistant to heat up to 240°C, is resistant to water, industrial solvents, acids and strong bases. Humble Bee Bio’s team are engineering yeast strains that can produce this polymer using fermentation. There's a ton of genetic potential in insects that could lead to performance materials that we just do not understand well today. For example, Raspy crickets make silk for shelter.
- Bacterial cellulose is another biomaterial that has performance characteristics. Modern Synthesis is using bacterial cellulose to “microbially weave” materials that allows for more design freedom in textiles and films. Bucha Bio’s bacterial cellulose has tensile strength higher than polyurethane, and is targeting textile markets. Polybion has built a first of a kind plant that will produce 1.1 million sq. ft. of bacterial cellulose per year, with production and polymerization only taking 20 days. They are partnering with the world's largest shoe manufacturer and three largest German auto companies. Simplifyber's cellulose is plant-based, but it is poured into a 3D-printed mold to make a one-piece sneaker, shirt or other clothing.
One interesting point to note is that in comparison to other deep tech startups, companies fermenting the future often have easier times pivoting in case their first venture doesn’t find product-market fit or expanding beyond it if it does. Their core competency is in the brewing process (whether that be their proprietary microbes, their specialized tanks, knowledge of the feedstock), not as much what comes after. So, many companies for instance in the mycelium space will make alternative meats of all kinds, leathers, and other textiles.
Here are some of the top companies in the above industries:
[1] 2018 paper and 2021 paper
[2] The following excerpt’s from this blog
[3] This excerpt from this article